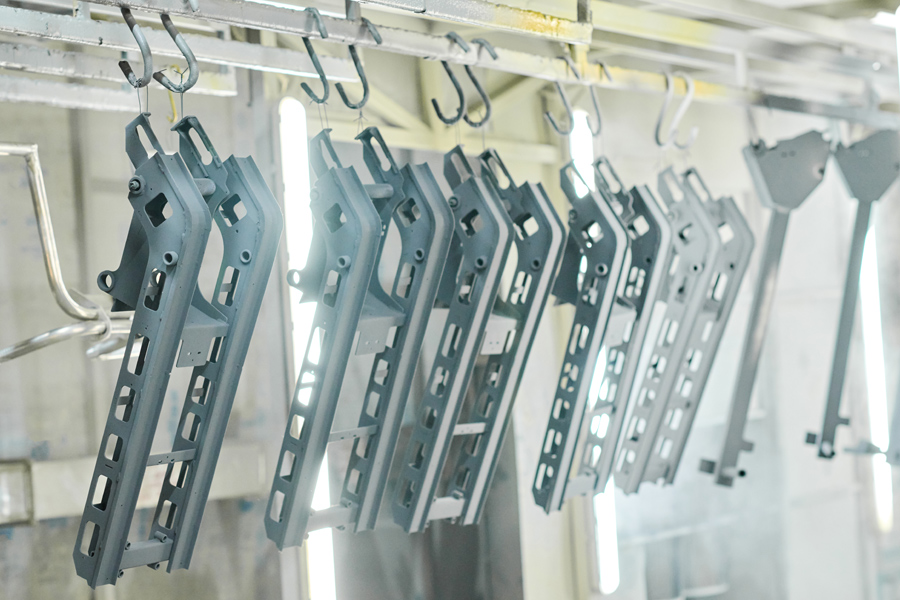
Electrocoating Complex Geometries
June 12, 2023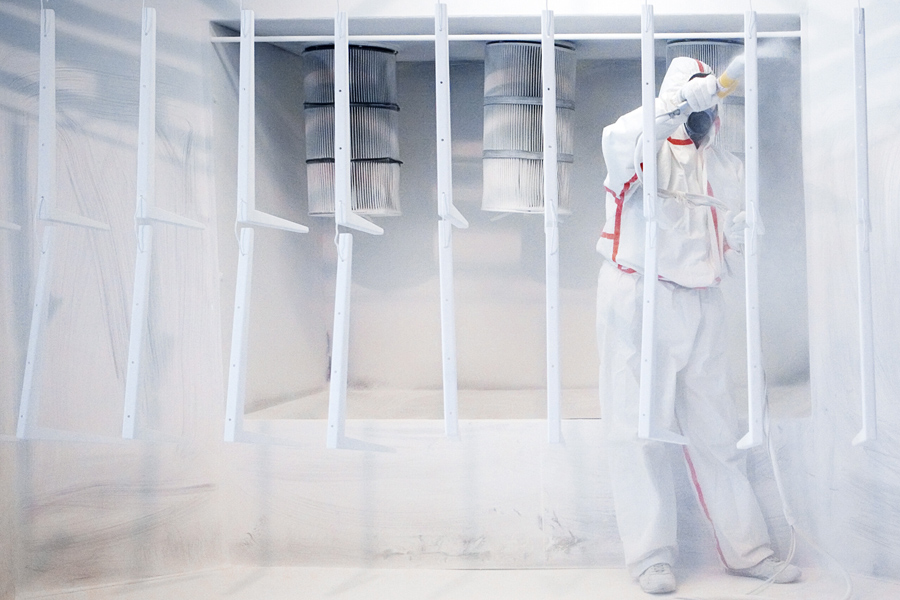
Experienced Parts Racking
July 10, 2023Preventing Outgassing in Powder Coating
Powder Coating is a Process, Powder Coaters Deliver Results
Powder coating involves applying a dry, electrically charged powder that adheres to most metallic substrates. After coating, parts are heated in an oven for curing. The process results in a hard, durable, and esthetically pleasing protective layer.
Powder coating is favored for its environmental friendliness, cost-effectiveness, and the ability to produce a protective, uniform coating with a wide range of colors and finishes. Ideal for metal parts, powder coating is widely used in industries like automotive, appliance, and machinery for its excellent durability and aesthetic versatility.
It is especially popular for use with automobile and bike parts, appliances, and machinery.
While powder coating is a great process, results are delivered by skilled powder coaters using proven protocols. As in all things, experience counts, and when you need the best call Great Dane Powder Coating at 724-537-9709 or visit our Contact Us page today.
Outgassing Ruins Powder Coating
At Great Dane Powder Coating, we have decades of experience, well-trained personnel, and cutting-edge methods that enable us to deliver high-quality results with every order. But all powder coaters are not made equal.
Outgassing is a typical problem you may run into, causing rework and additional expense to get your parts run done right.
This phenomenon occurs during the curing process of powder coating, especially when coating porous materials such as cast metals. Believe it or not, metals can absorb gases and air during manufacturing. When the material is heated during the curing process, these trapped gases attempt to escape from the substrate and pass through the powder coating.
This outgassing creates cosmetic and structural defects in the finished coating. The most common defect is the formation of bubbles or pinholes on the surface of the coating, creating an uneven finish. These defects can compromise the coating’s integrity, reducing its corrosion and wear resistance. This can shorten the lifespan of the coating and, in turn, the item it’s protecting.
Methods To Prevent Outgassing in Professional Powder Coating
Outgassing can be mitigated in several ways, such as outgassing the material before powder application (pre-baking), using a powder that’s formulated to allow gases to escape before it fully cures (outgas forgiving powder), or using a two-coat process where the first coat allows for outgassing and the second seals the surface. Let’s take a quick look at each:
Prebaking: This involves heating the part to be coated prior to applying the powder coat. The heat will cause any gases trapped within the substrate to be released.
Choosing the right powder: Certain powder formulations are designed to be more tolerant to outgassing. These powder coatings are generally referred to as ‘outgas forgiving’ or ‘low density’ powders.
Proper preparation of the substrate: This is the most crucial step in any coating process. The substrate needs to be cleaned thoroughly. Any contaminants such as oils, greases, oxides, or other residues need to be removed.
Porous Fillers: In the case of porous castings, filling the substrate with a suitable material can prevent outgassing. This filler hardens and blocks the pores, preventing the trapped gases from causing defects during the curing process.
Adjusting curing process: It’s important to monitor and adjust the curing process carefully. Sometimes, increasing the curing time can allow more time for the gasses to escape before the coating fully hardens.
Two-coat process: Apply a first coat of powder and partially cure it, but not to the point of full flow and crosslink. This forms a skin on the surface but does not completely cure the powder. This allows gases to escape during the second full cure cycle, resulting in a smooth finish.
Using Outgassing Additives: There are special additives that can be mixed with the powder to reduce outgassing. These are designed to form a microscopic network of channels in the coating, providing a path for the gas to escape without forming visible defects in the surface of the coating.
Every situation might require a different approach and sometimes a combination of methods works best to prevent outgassing in professional powder coating.
Learn how Great Dane Powder Coating works to deliver the best results, cost-effectively. Call us at 724-537-9709 or visit our Contact Us page today.
Delivering Coating Excellence for over 29 Years!
At Great Dane Powder Coating, Inc., we have more than a quarter century of experience under our belts. We offer the benefits of a cutting-edge facility and high-end equipment for providing exceptional results.
It’s no wonder that we are trusted by industries across the country to deliver highly durable coatings on a wide variety of parts.
When you want affordable, reliable, and outstanding results, give us a call at 724-537-9709 or visit our New Powder Coating Customer page today.
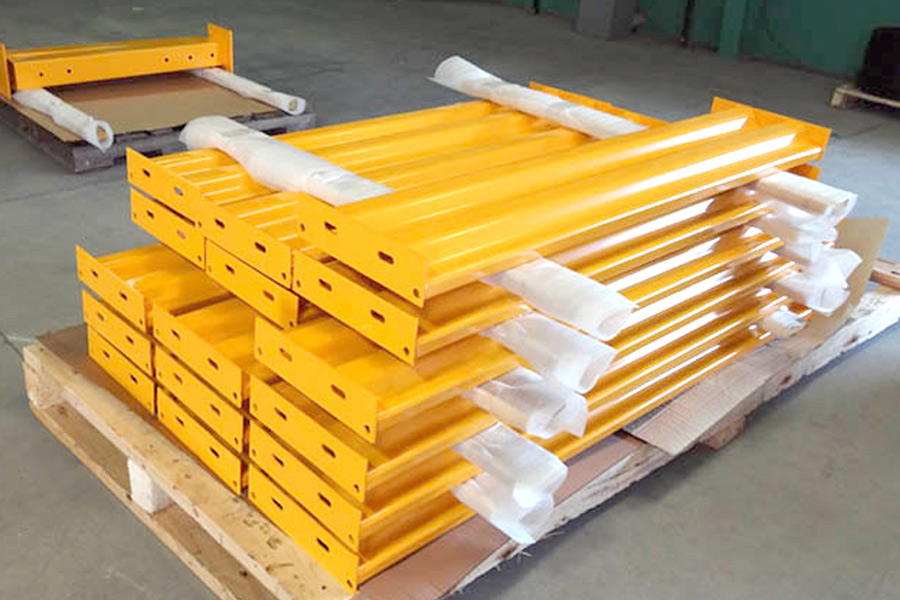
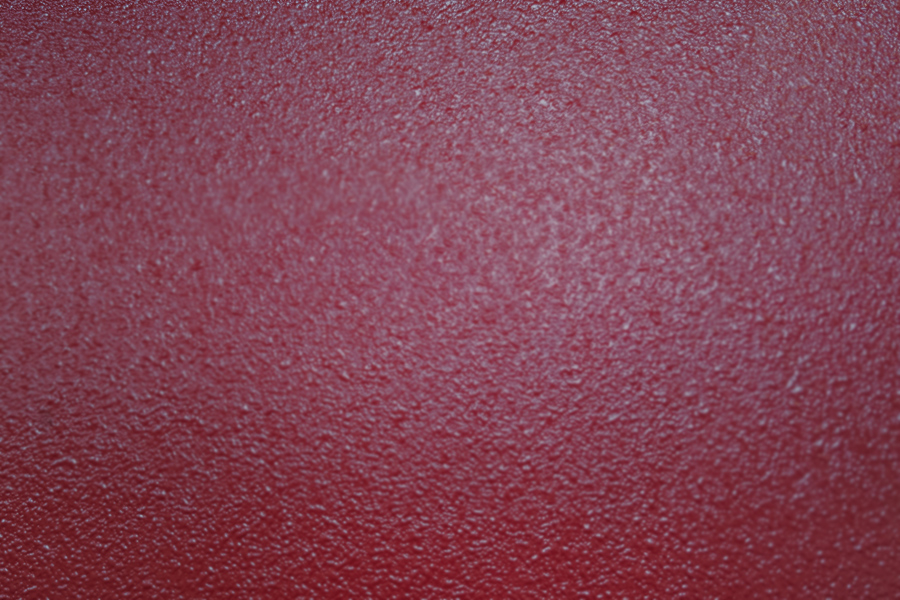
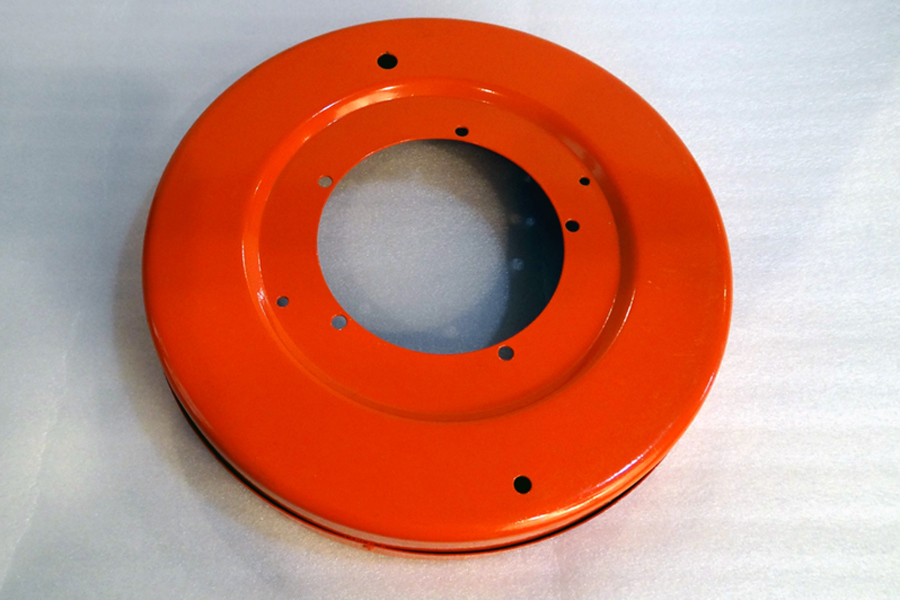
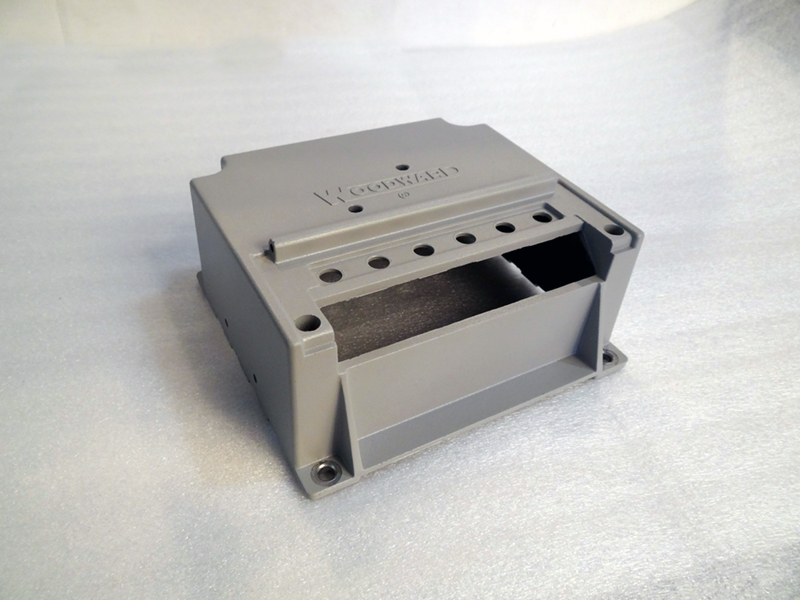
Interested?
Call us today at 724-537-9709 or click a button below.