
Powder Coating Aluminum Parts and Extrusions
March 11, 2024Powder Coating and Electrophoretic Painting: Benefits, Applications, and Industry Insights
October 22, 2024Cost-Effective Solutions for Coating Aluminum Parts and Assemblies
Electrocoating is the Answer
At Great Dane Powder Coating in Loyalhanna, PA, our advanced coating technologies deliver precision and durability at affordable prices.
Among our specialized services, electrophoretic deposition is a standout choice. Also called e-coating, this technology is perfect for enhancing the performance and lifespan of aluminum parts and assemblies.
E-coating not only augments aluminum’s inherent corrosion resistance but also offers cost-effective solutions tailored to a variety of industrial needs.
E-coating for aluminum offers a protective layer that combines aesthetics with robust environmental protection. Whether you’re looking to improve durability, reduce maintenance costs, or achieve a specific visual look, our e-coating process ensures that every aluminum part meets the highest standards of quality and performance.
How Does e-Coating for Aluminum Work?
Electrophoretic deposition is a method of coating aluminum parts through an electrically charged process. In e-coating, the aluminum component acts as an electrode when submerged within a water-based solution that contains dispersed paint or epoxy particles. When an electrical charge is applied, the particles migrate towards the aluminum part, uniformly adhering to its surface.
One stand-out advantage of e-coating is its ability to create a uniform coating even in recessed or intricately shaped areas.
The result is a thin, even layer of coating that is heat-cured to form a tough, protective finish. This process ensures complete and consistent coverage while providing excellent corrosion resistance.
Benefits of e-Coating for Aluminum
E-coating improves the basic corrosion resistance of aluminum, providing a barrier that extends the durability and lifespan of aluminum parts. E-coating safeguards against environmental threats such as moisture, salt spray, and various chemicals. The seamless bond formed between the e-coat and the aluminum substrate effectively minimizes exposure to oxidative elements, helping prevent corrosion and wear over time.
E-coating is also known for its cost-effectiveness. The process is highly efficient, minimizes waste, and ensures thorough coverage. This efficiency translates into lower operational costs and extended parts lifecycle.
Aesthetically, e-coating is available in a range of gloss levels and textures, enabling manufacturers to achieve a desirable finish. This makes it suitable for a wide array of applications, from automotive components to decorative items, where appearance is as critical as performance.
Industry Applications
In the automotive sector, aluminum is widely used to reduce weight and improve fuel efficiency. Common parts using aluminum include engine components like cylinder heads, pistons, and engine blocks. Transmission housings, heat exchangers, and suspension parts are often made of aluminum. From body panels to wheels and brakes, the trend toward aluminum use in automotive manufacturing continues to grow.
The ability of e-coating to penetrate complex shapes and crevices makes it particularly useful for ensuring that every aluminum component is uniformly protected against rust and degradation.
Beyond automotive applications, e-coating is also prevalent in the electronics industry. Here, the process is employed to coat critical aluminum components like enclosures and casings, heat sinks, connectors and switches, mounting brackets and hardware. E-coating can be crucial in protecting devices exposed to harsh conditions, such as outdoor communication equipment and industrial sensors, where reliability over long periods is important.
The architectural field also benefits from e-coating, especially in the production of aluminum building facades, window frames, and structural components. The ability to customize the finish allows architects and designers to achieve both the desired durability and aesthetics. This makes e-coating an attractive choice for commercial and residential buildings where varying climates and environmental stresses must be taken into account.
Electrocoating is a Great Choice for Aluminum Parts
Electrocoating stands out for its unique advantages, especially when applied to aluminum parts. Compared to anodizing that changes the surface structure of aluminum to create a hard layer, e-coating deposits a uniform protective layer that adheres well to the substrate. This uniformity is important for complex shapes where ensuring complete coverage can be challenging.
The protective layer formed by e-coating is thin yet durable, which helps in maintaining the lightweight nature of aluminum without compromising on protection or functionality. This makes e-coating an excellent choice for aluminum parts, balancing performance with aesthetics.
Give Great Dane a Call Today for Your Electrocoating Needs
For manufacturers looking to optimize the longevity and appearance of their aluminum products, adopting e-coating can be a pivotal step towards achieving superior quality and performance.
When you want affordable, reliable, and outstanding results, give us a call at 724-537-9709 or visit our New ElectroCoating Customer page today.
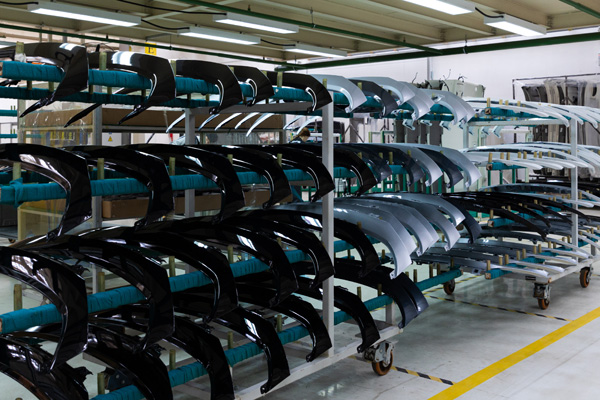
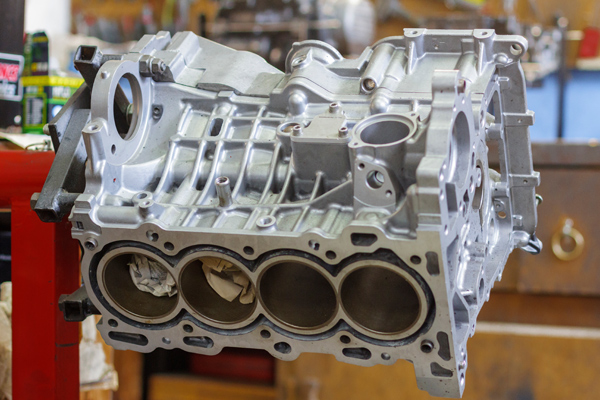
Interested?
Call us today at 724-537-9709 or click a button below.