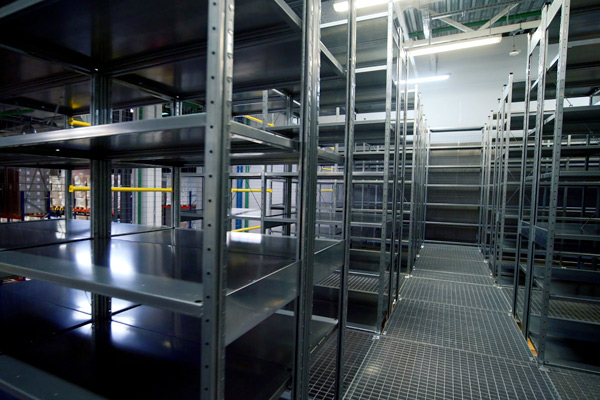
E-Coating for the Metal Furniture and Fixtures Market
February 21, 2024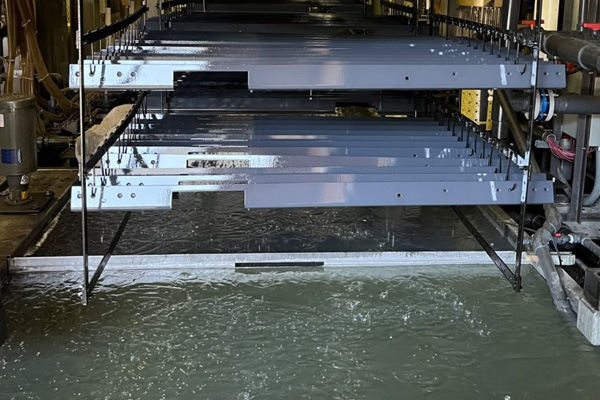
Cost-Effective Solutions for Coating Aluminum Parts and Assemblies
April 17, 2024Powder Coating Aluminum Parts and Extrusions
An Experienced Team and a Proven Process Make all the Difference
Yes, powder coating offers a durable and attractive finish for aluminum parts and extrusions. This process not only enhances the visual appeal of aluminum but also significantly boosts its resistance to corrosion, impact, and wear, making it an ideal choice for a variety of applications.
From automotive components to architectural frameworks, powder coating aluminum parts ensures they stand up to the demands of use and time, all while embracing a variety of eye-catching colors. The value of powder coating is its ability to provide exceptional durability and an aesthetic boost to aluminum surfaces, qualities sought after in today’s market.
The Importance of Expertise
Achieving a great powder-coated finish is challenging, involving a series of steps that each play a role in the outcome. This complexity underscores the need for both an experienced team and a proven process.
It starts with surface preparation, then powder application, curing, and quality control. Each step requires an understanding of the materials involved, as well as the technical nuances that can influence the results of the finish.
Only through years of experience can powder coaters develop the eye and skill set needed to prepare surfaces to perfection, recognizing the cues that indicate a part is ready for the next stage.
The application of the powder itself demands precision and control. The electrostatic spray gun must be wielded by someone who understands how to achieve an even coating, adjusting for the shape and size of the part and the type of powder being used.
And when it comes to curing – a phase where the powder transforms into a durable finish – the ability to meticulously control temperature and time is paramount. These aspects highlight how an experienced team with a commitment to quality is indispensable in achieving the best possible results.
Surface Preparation: The Foundation of Exceptional Powder Coating
Surface preparation is the unsung hero of the powder coating process, setting the stage for the adhesion, durability, and overall quality of the finish. This critical first step ensures that aluminum parts and extrusions are perfectly primed for powder coating.
The role of surface preparation is to cleanse the aluminum of impurities that could hinder the powder coating’s adherence and to texture the surface for better adhesion. The processes can vary significantly based on the condition of the aluminum parts and the quality standards desired for the final product. Techniques range from mechanical methods like scraping and grinding to remove old coatings, to chemical treatments that cleanse and etch the surface.
One of the most effective methods for preparing aluminum surfaces is sandblasting or shot blasting, which not only removes existing coatings, debris, oil, and grime but also effectively “roughens” the surface.
After the aluminum has been thoroughly cleaned and textured, it must be completely dried. Any moisture remaining on the surface can cause imperfections in the coating, such as bubbling or poor adhesion.
Powder Application: The Art of Precision and Control
At this stage, powder coating is applied using an electrostatic spray gun. This tool charges the powder particles positively, ensuring they adhere to the electrically grounded aluminum surface. The skill of the operator becomes critical here; only with experience can an even distribution of powder across a complex part be achieved. It’s a delicate balance of managing the flow of powder, the distance of the gun from the surface, and the evenness of the coat that defines the quality of the finish.
Curing: The Crucial Transformation Phase
Curing is where the applied coating transitions from a soft layer to a hard, durable finish through the application of heat in a curing oven. The temperature and duration of curing must be carefully controlled to match the powder formulation and the dimensions of the part. Typically, curing temperatures do not exceed 390°F (200°C), with a general timeframe of about 10-15 minutes, although these parameters can vary based on the specifics of the job. Getting it right is crucial for ensuring that the powder melts, flows, and cross-links to form a uniform, robust coating that adheres strongly to the aluminum substrate.
Too little heat or insufficient time can result in an under-cured coating that lacks durability, while excessive heat or too much time can lead to discoloration or a compromised finish. An experienced team can ensure that each part emerges from the oven with a finish that meets the highest standards.
Quality Inspection: Ensuring Excellence
Following the curing process, quality control (QC) technicians engage in a variety of inspection techniques to evaluate the coating, including visual inspections and more detailed tests like the crosshatch test, which assesses cured adhesion quality.
The role of experienced QC staff cannot be overstated, as their expertise enables them to recognize the smallest defect, as well as the subtle signs that a part’s coating is flawless. This dedication to quality reflects the overall commitment to excellence that characterizes the entire powder coating process, from surface preparation through to the final QC check, ensuring that each coated part or extrusion performs its function beautifully and will last for years to come.
Advantages of Choosing an Experienced Team and a Proven Process
Selecting a provider with a proven process for powder coating aluminum parts and extrusions is instrumental in unlocking the benefits this finishing method offers. An experienced team brings a depth of knowledge and a breadth of skills that significantly impact the quality, durability, and appearance of the final product.
One of the primary advantages of working with a seasoned team is the enhanced corrosion resistance and impact durability of the coated parts. Powder coating improves the aluminum’s resilience, making it better suited for challenging environments and extending its service life. Moreover, the ability to apply a wide range of colors, including custom hues, allows for greater creativity and branding opportunities, ensuring that the final product is not only robust but also visually appealing.
When you want affordable, reliable, and outstanding results, give us a call at 724-537-9709 or visit our New Powder Coating Customer page today.
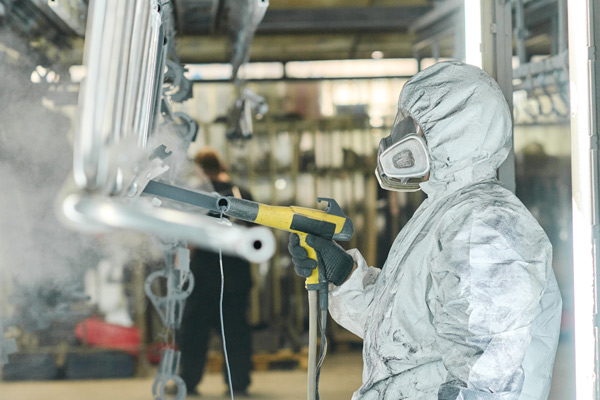
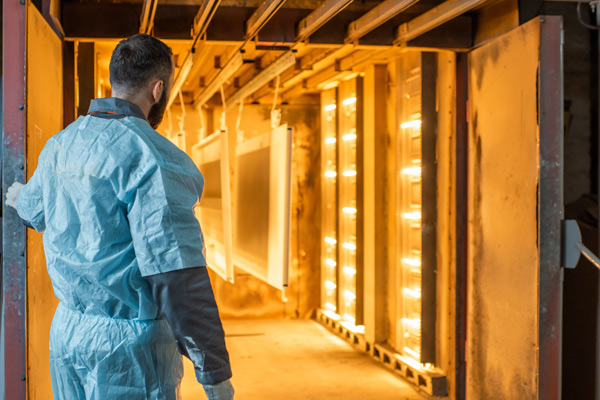
Interested?
Call us today at 724-537-9709 or click a button below.