
Preventing Outgassing in Powder Coating
June 21, 2023
Electrocoating — a Great Process for Coating Large Part Orders Quickly
July 24, 2023Experienced Parts Racking
A Critical Part of Successful Powder Coating
Proper racking is an essential component of successful powder coating projects. Racking optimizes the positioning of each piece to promote uniform powder deposition, even in complex geometries.
Experienced racking enhances the efficiency of powder coating by maximizing the number of items that can be coated per batch and speeding up turnaround times. Properly designed racks also facilitate good grounding and minimize contact points. The first is essential in the electrostatic application of the powder, the second reduces the areas on the parts that don’t receive coating.
In contrast, poor grounding can lead to uneven powder application, compromising the quality and durability of the finish.
The Cost of Poor Racking and the Benefits of Good Racking
One of the most common areas of waste in a powder system is poor racking. When racking is not properly executed, it can result in a range of issues that impact the quality of the coating process.
Some of the most common problems with inexperienced racking include more rejects and wasted powder. This results in longer processing times and slower turnaround.
To address these challenges, it is crucial to implement good racking schemes that hold the parts steady, provide good grounding, and maximize the available line space and spray gun capacity. Good racking designs ensure consistent positioning of the parts, reduce excess space, and offer easy access to all surfaces.
With good racking, the benefits include:
Improved first-pass yield: Properly designed racks enable consistent powder application, reducing the likelihood of defects and increasing the first-pass yield.
Enhanced production efficiency: Good racking allows for higher part density, maximizing the number of parts that can be coated per batch and reducing processing times.
Cost savings: By optimizing the racking arrangement, coating operations can achieve better throughput and reduce waste, resulting in cost savings.
Principles for Effective Racking Design
To achieve successful powder coating, it is important to consider several principles when designing racks:
Good density: Parts should be grouped closely together, reducing the space around them and maximizing the ratio of metal to air. However, there should be enough space to ensure easy and complete coverage of each part.
Accessibility and visibility: Parts should be positioned in a way that allows for easy access and visibility during the coating process. This ensures that all surfaces are adequately coated.
Stability and consistency: Racks should hold the parts in a stable and consistent position, minimizing movement and ensuring uniform powder application.
Clean contacts: Contacts between the parts and racks must always be clean to prevent insulation from earth ground by coating build-up.
Following these principles helps ensure efficient and effective racking, resulting in high-quality powder coating jobs.
Investing in the Right Racking Scheme
Some powder coating companies hesitate to invest in proper tooling or evaluate different racking options due to concerns about cost and complexity. However, failing to do so can result in significant losses and missed opportunities for improvement. Evaluating the options and choosing the right racking scheme always leads to improved throughput for client projects.
The ROI can be significant, especially for high-volume parts with frequent runs. Even if the volume is low and parts are not run frequently, investing in the right tooling can still provide long-term benefits. Good racking improves the first pass yield, reduces rejects, and allows for more parts to be processed efficiently.
Summary
Experienced parts racking by companies like Great Dane Powder Coating is a critical aspect of successful powder coating. By implementing proper racking designs, coating operations can achieve uniform powder deposition, improve throughput, and reduce costs.
Learn how Great Dane Powder Coating works to deliver the best results, cost-effectively. Call us at 724-537-9709 or visit our Contact Us page today.
Delivering Coating Excellence for over 29 Years!
At Great Dane Powder Coating, Inc., we have more than a quarter century of experience under our belts. We offer the benefits of a cutting-edge facility and high-end equipment for providing exceptional results.
It’s no wonder that we are trusted by industries across the country to deliver highly durable coatings on a wide variety of parts.
When you want affordable, reliable, and outstanding results, give us a call at 724-537-9709 or visit our New Powder Coating Customer page today.


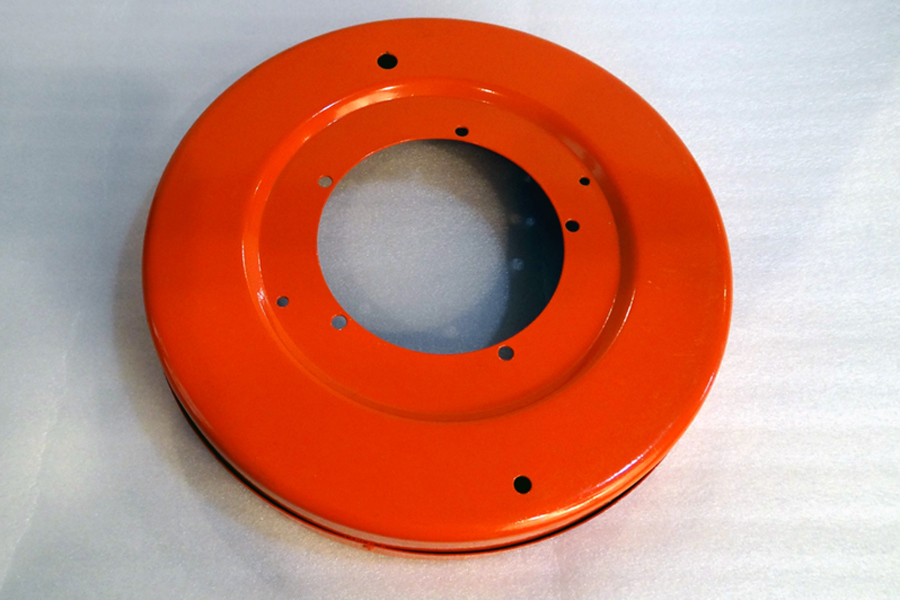
Interested?
Call us today at 724-537-9709 or click a button below.