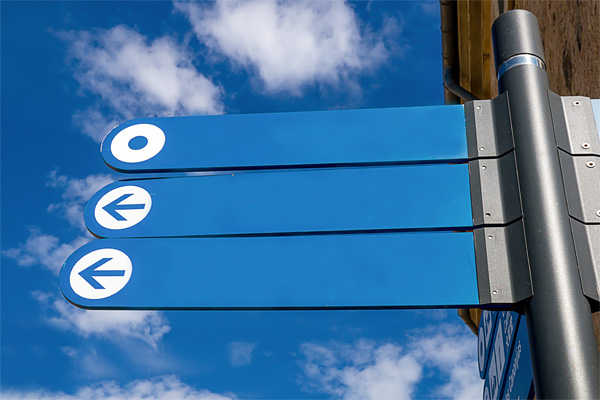
The Benefits of Powder Coating in Architectural Signage
January 4, 2024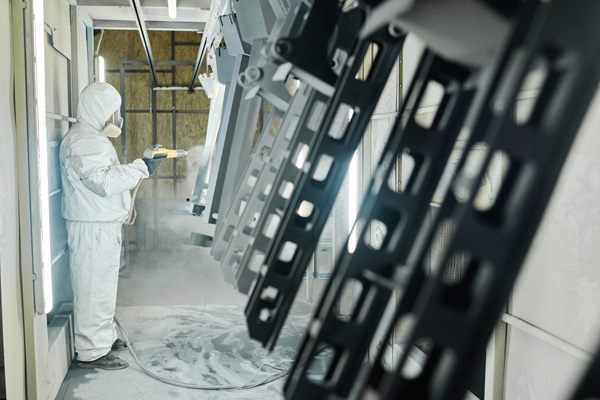
Powder Coating vs. Parts Painting
February 9, 2024E-Coating for Heat Exchangers and HVAC Coils
From Corrosion Resistance to Uniform Coating
In manufacturing heat exchangers and HVAC coils, the requirement for precise and durable coating technology is critical. Electrophoretic coating, commonly known as e-coating, has emerged as a widely adopted solution, offering unmatched benefits in these applications.
Let’s take a look at the basics of e-coating and its pivotal role in enhancing the performance and longevity of heat exchangers and HVAC coils.
What is E-Coating?
E-coating involves the application of paint or resin to a surface using an electrical current. This process allows for the controlled deposition of the coating material, ensuring uniform thickness even over complex and hard-to-reach areas.
In e-coating, the substrate, like the coil assemblies used in heat exchangers or HVAC systems, is immersed in a bath containing a water-based solution of paint or resin. This solution is composed of charged paint particles suspended in a solvent. When an electrical current is applied, these charged particles are attracted to the oppositely charged surface of the substrate, adhering to it in a uniform layer.
The thickness of this coating is precisely controlled by adjusting the voltage and duration of the electric current. The process is self-limiting, meaning that as the coating builds up, it insulates the substrate and naturally prevents over-deposition, ensuring a uniform thickness throughout the coated surface. The consistency and control possible with e-Coating is crucial for heat transfer efficiency and durability.
The Significance of Uniform Coating
In the heating, ventilation, and air conditioning (HVAC) industry, the uniformity of the coating is vital. E-coating excels in applying a uniform layer over intricate surfaces and hard-to-reach areas.
This uniformity is essential for maintaining consistent heat transfer efficiency and prolonging the durability of the coils and exchangers.
Corrosion Resistance: A Key Benefit
Corrosion is a costly issue in the HVAC industry. Heat exchangers, especially in HVAC equipment, are prone to corrosion due to their exposure to various environments. E-coating significantly enhances the corrosion resistance of these components, ensuring they can withstand diverse environmental conditions, from coastal areas to industrial settings.
E-coating delivers protection against:
- Atmospheric Corrosion
- Chemical Corrosion
- Salt Spray Corrosion
- Galvanic Corrosion
- Rust due to Condensation and Humidity
- Thermal Stress
E-Coating Process
The e-coating process involves several key steps:
Pre-treatment: This includes cleaning and phosphating the heat exchanger surface, ensuring that it’s free from contaminants that could affect the coating process.
Electrocoat Bath: The component is immersed in a bath containing paint emulsion, solvents, and deionized water. A DC rectifier controls the amount of paint deposited, with cathodic deposition offering superior corrosion and UV resistance.
Post-Coating Rinsing: Excess paint is removed, enhancing both efficiency and aesthetics.
Thermal Curing: Involves using a bake oven to cure and cross-link the paint film, solidifying the coating’s protective properties.
Materials in E-Coatings
Electrocoatings are typically made from polymeric resins, solvents, diluents, and pigments. The resins are crucial for corrosion protection and UV durability, while pigments and solvents contribute to the coloring, gloss, and smooth appearance of the end product.
Advantages of E-Coating
E-coating offers several advantages over traditional coating methods:
- High Corrosion Protection: It can withstand over 1000 hours in a salt spray test, according to ASTM B117 standard.
- Uniform Coating: Variance is minimal, within 1-2 microns across any surface complexity.
- Eco-Friendly: Free from heavy metals, low in hazardous air pollutants (HAPs), organic solvents, and volatile organic compounds (VOCs).
- Aesthetic Quality: Provides a smooth and visually appealing finish.
E-coating represents a significant advancement in the coating technologies used in the HVAC and heat exchanger industries. Its ability to provide uniform, durable, and corrosion-resistant coatings in an eco-friendly manner positions it as an essential process for industrial clients who demand high quality and performance. The integration of e-coating in manufacturing practices not only maximizes performance but also aligns with sustainable and environmentally conscious approaches, making it a preferred choice for the future.
Delivering Coating Excellence for over 30 Years!
At Great Dane Powder Coating, Inc., we have more than three decades of experience under our belts. We offer the benefits of a cutting-edge facility and high-end equipment for providing exceptional results.
It’s no wonder that we are trusted by industries across the country to deliver highly durable coatings on a wide variety of parts.
When you want affordable, reliable, and outstanding results, give us a call at 724-537-9709 or visit our New ElectroCoating Customer page today.
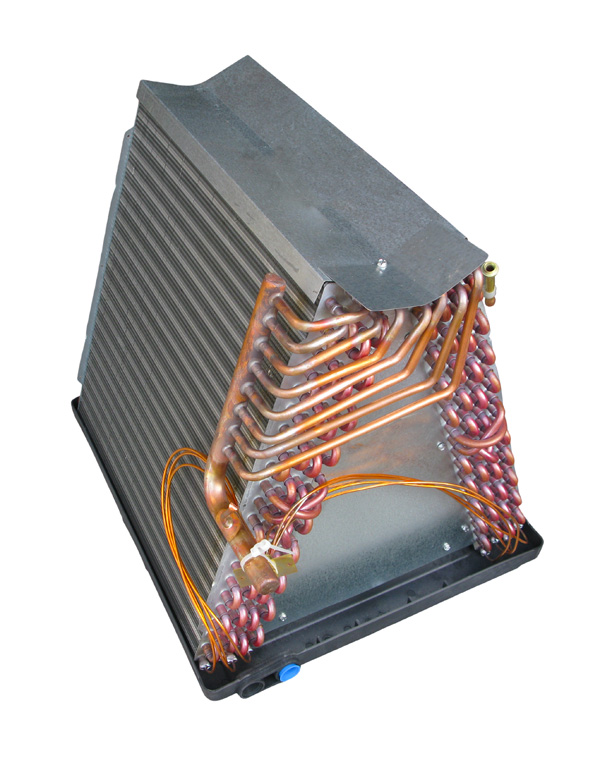
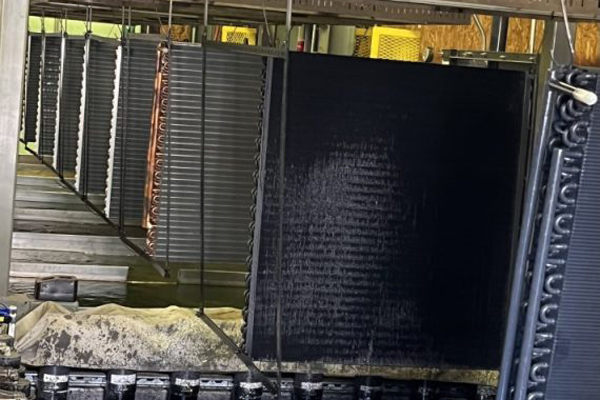
Interested?
Call us today at 724-537-9709 or click a button below.